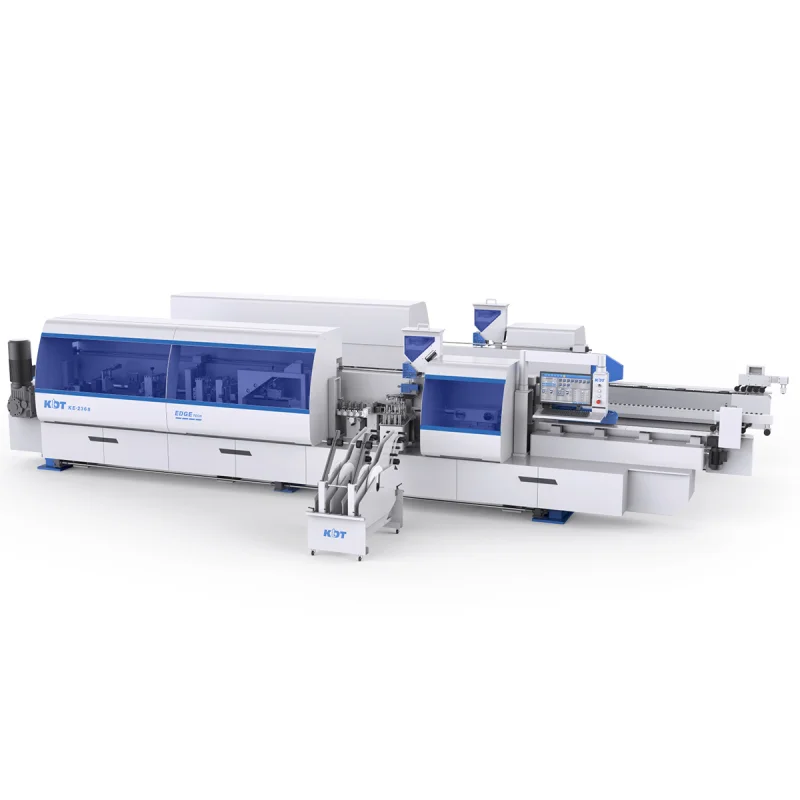
Technical Specifications
Feed speed, m/min | 20-26 |
Machine units | 1. Joint joint. 2. Clamping unit. 3. Facing unit. 4. The first milling unit for removing overhangs. 5. The second milling unit for removing overhangs. 6. Scraping unit with radius knives. 7. Scraping unit with flat knives. 8. Grooving knot from 2 sides. 9. Polishing unit. |
Minimum part size, mm | 285x285 |
Edge thickness, mm | 0.4-3 |
Workpiece thickness, mm | 9-60 |
Workpiece width, mm | ≥ 285 |
Workpiece length, mm | ≥ 285 |
Total power, kW | 48 |
Working pressure, MPa | 0.6 |
Dimensions LxWxH, mm | 8538x4300x1825 |
Weight, kg | 7200 |
Double Sided Edge Banding Machine KE-2368JHSKCAD
Purpose :
Double-sided automatic edge banding machine KE-2368JHSKCAD is designed for simultaneous lining of straight edges of furniture panels and blanks with synthetic roll material on both sides. It is used at furniture factories producing serial furniture. Machine components Jointing unit. Clamping unit. Facing unit. The first milling unit for removing overhangs. Second milling unit for removing overhangs. Scraping unit with radius knives. Scraping unit with flat knives Grooving unit on 2 sides. Polishing unit.
Distinctive features :
Feed speed 20-26 m/min; Magazine for edging material for 4 types of edges; Automatic stops in conveyor pads for positioning the part at 90 °; A jointing unit with a double chopper for high-quality preparation of the workpiece before gluing; Upper glue bath for working with EVA/PUR adhesives; A pressure tape instead of rollers guarantees precise positioning of the part at all stages of edge processing at a speed of 26 m/min; “Touch screen” control panel based on WINDOWS 10; Pneumatic adjustment for different edge thicknesses from the control panel; Programming technological breaks in heating the glue bath; Individual frequency converter for each working unit; Lighting in the protective cabin; For safety, the machine is equipped with an electronic cabin door locking system; The mechanism for raising/lowering the clamping beam is equipped with an electric drive, which ensures quick and accurate installation to the required thickness of the part; A locating ruler with a digital counter guarantees quick and accurate setting of the required removal on the part during milling at the jointing unit; A pneumatic curtain on the glued application roller prevents it from becoming dirty; Adjustment of front and rear edge overhangs from the control panel.

machine bed - The bed of the edgebanding machine has the shape of a rigid box with the necessary stiffening ribs, which guarantees the exact location of all components throughout the entire service life .

PC control panel - The machine is controlled using an industrialpersonal computerwith a “Touch screen” system. The on/off icons for components and assemblies on the display are intuitive and do not require special skills to operate the machine .

technological breaks - Possibility of programming technological breaks in heating the glue bath .

dispenser rod - The workpiece feed dispenser rod controls the minimum distance between workpieces, preventing damage to machine components during operation .

edge feed store - The edge feed magazine for 4 types of edges simplifies and speeds up the process of changing edges and switching to another thickness, width, color .

conveyor stop system - Automatic stops in the conveyor pads push the panel and enable precise 90°positioning .

jointing unit - The jointing unit is equipped with a double crusher, which allows you to format the panel, removing up to 5 mmmaterial on each side and formats without damaging the pre-processed side .

heating the end of the workpiece - Preheating of the workpiece end for better adhesion .

Clamping unit - The pressure unit consists of 5 rollers, which are driven pneumatically, which guarantees an even distribution of forces on the edge during gluing .

upper glue bath - The machine is equipped with an automatictop glue tank for PUR/EVA gluewith pre-melt glue, with a capacity of 5 liters. The glue is supplied in doses and does not overheat during machine downtime .

trimming unit - The end trimming unit is equipped with two high-frequency electric motors, and the saw units move along special linear guides. The unit is equipped with an automatic lubrication system for the guides .

milling unit - The milling unit consists of two high-frequency electric motors equipped with radius cutters, which allow processing edge material with a thickness of 0.4 - 3.0 mm .

radius cycle - Radial scraping with two carbide radius knives, which, after milling an edge 2.0 mm thick, remove a thin layer from the milled part of the edge, resulting in a smooth machined surface .

flat scraper - The direct scraping unit is equipped with two carbide straight knives (glue scraper), which process the edges at the joints with the part .

grooving unit - The grooving milling unit is equipped with a groove saw with carbide tips for milling a groove for the rear wall .

polishing unit - A double polishing unitpolishes the processed part of the edge; high quality is achieved through an oscillation system driven by pneumatic cylinders. To impart a final shine to the edge, a unit for applying polishing liquid is installed .

pressure tape - A pressure belt instead of rollers guarantees precise and reliable positioning of the workpiece during all stages of edge processing at a speed of 26 m/min .

encoder - The encoder on the mechanism for raising/lowering the clamping beam allows you to automatically position the crossarm to the thickness of the part set on the control panel .

automatic lubrication of the end assembly - The centralized lubrication unit automatically lubricates the guides of the trimming unit .

electrical components according to CE standard - Electrical components are made in accordance with CE standards .
Technical Specifications
Feed speed, m/min | 20-26 |
Machine units | 1. Joint joint. 2. Clamping unit. 3. Facing unit. 4. The first milling unit for removing overhangs. 5. The second milling unit for removing overhangs. 6. Scraping unit with radius knives. 7. Scraping unit with flat knives. 8. Grooving knot from 2 sides. 9. Polishing unit. |
Minimum part size, mm | 285x285 |
Edge thickness, mm | 0.4-3 |
Workpiece thickness, mm | 9-60 |
Workpiece width, mm | ≥ 285 |
Workpiece length, mm | ≥ 285 |
Total power, kW | 48 |
Working pressure, MPa | 0.6 |
Dimensions LxWxH, mm | 8538x4300x1825 |
Weight, kg | 7200 |