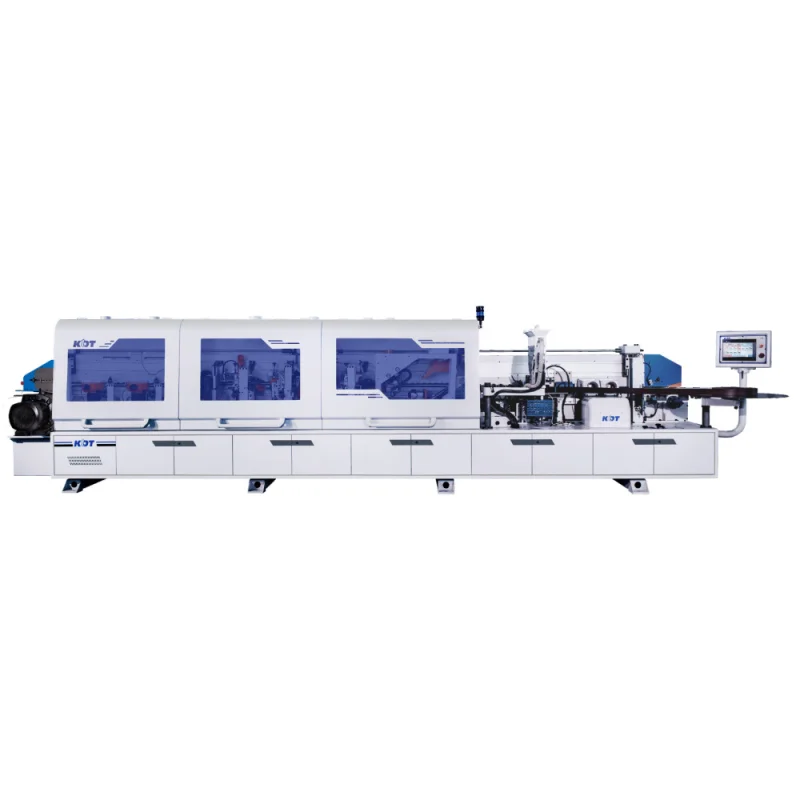
Technical Specifications
Feed speed, m/min | 20-26 |
Machine units | 1. Joint joint. 2. Clamping unit. 3. Facing unit. 4. The first milling unit for removing overhangs. 5. The second milling unit for removing overhangs. 6. The first scraping unit with radius knives. 7. Polishing unit with oscillation. 8. Double horizontal grooving unit. |
Minimum part size, mm | 120x95 |
Edge thickness, mm | 0.4-3 |
Workpiece thickness, mm | 10-60 |
Workpiece width, mm | ≥ 95 |
Workpiece length, mm | ≥ 120 |
Total power, kW | 34,75 |
Working pressure, MPa | 0.6 |
Dimensions LxWxH, mm | 7346x990x1700 |
Weight, kg | 2300 |
Automatic edge banding machine KE-386JKM
Purpose :
High-speed automatic edge banding machine KE-386JKM is designed for simultaneous banding of straight edges of furniture boards and blanks with synthetic roll material. The machine is designed for unidirectional or bidirectional cutting of a groove up to 20 mm deep in the production of door panels. Machine components Joint knot. Clamping knot. Ending knot. The first milling unit for removing overhangs. The second milling unit for removing overhangs. The first scraping unit with radius knives. Polishing unit with oscillation. Double horizontal groove knot.
Distinctive features :
High feed speed 20-26 m/min; Upper glue bath; Pressing belt instead of rollers guarantees precise positioning of the part at all stages of edge processing at a speed of 26m/min; Lamp for preheating the end face of the workpiece; Control panel "Touch screen"; Built-in waypoint control for contactless control of processing units; Possibility of programming technological breaks of the glue bath; Implemented the ability to automatically reconfigure the traverse to the size set on the control panel using the encoder.

machine bed - The bed of the edge banding machine has the form of a rigid box with the necessary stiffening ribs, which guarantees the exact location of all nodes during the entire period of operation .

Remote Control - The machine is controlled using a special remote control equipped with an industrial display with a “Touch screen” system .

technological breaks - Possibility of programming technological interruptions of glue bath heating .

joiner unit - The jointing unit is equipped with two high-frequency motors, which ensures high-quality processing of the end face of the material before gluing the edge. Pre-milling copes with the “step” from the scoring saw, chips .

billet end heating - Preheating the end face of the workpiece for better adhesion .

Clamping unit - The pressing unit consists of 5 rollers, which are driven by pneumatics, which guarantees an even distribution of forces on the edge during gluing .

upper glue bath - Upper glue bath with pre-melted glue, capacity 5 litres. Glue is dosed and does not overheat during machine downtime. The viewing window allows you to control the presence of glue. Warm-up time and readiness for work 15 minutes .

facing unit - The end trimming unit is equipped with two high-frequency electric motors, and the movement of the saw units is carried out along special linear guides. The unit is equipped with an automatic lubrication system for the guides .

milling unit - The milling unit consists of two high-frequency electric motors equipped withdiamond radius cutters, which allow processing edge material with a thickness of 0.4 - 3.0 mm .

radius cycle - Radial scraping with two carbide radius knives, which, after milling a 2.0 mm thick edge, remove a thin layer from the milled part of the edge, as a result we get a smooth machined surface .
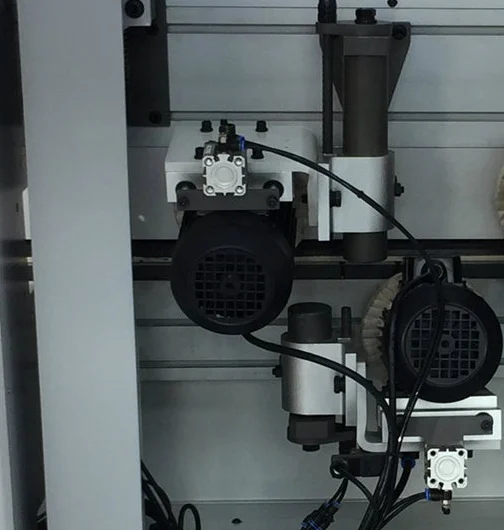
polishing unit - The polishing unit polishesthe processed part of the edge, high quality is achieved throughan oscillation system driven by pneumatic cylinders .

Double grooving knot - The double horizontal grooving unit is equipped with two carbide-tipped grooving saws for door groove milling .

pressure tape - The pressure band instead of rollers guarantees precise and reliable positioning of the workpiece in all stages of edge processing at a speed of 26 m/min .

encoder - The encoder on the mechanism for raising/lowering the clamping traverse allows you to automatically position the traverse to the thickness of the part set on the control panel .

automatic lubrication of the end assembly - The centralized lubrication unit automatically lubricates the guides of the trimming unit .

electrical components according to CE standard - The electrical components are made in accordance with CE standards .

Noise isolation - The doors of the machine cabin are sheathed with a layer of sound insulation made from foamed polyurethane foam, which allows you to achieve comfortable work with the equipment .
Technical Specifications
Feed speed, m/min | 20-26 |
Machine units | 1. Joint joint. 2. Clamping unit. 3. Facing unit. 4. The first milling unit for removing overhangs. 5. The second milling unit for removing overhangs. 6. The first scraping unit with radius knives. 7. Polishing unit with oscillation. 8. Double horizontal grooving unit. |
Minimum part size, mm | 120x95 |
Edge thickness, mm | 0.4-3 |
Workpiece thickness, mm | 10-60 |
Workpiece width, mm | ≥ 95 |
Workpiece length, mm | ≥ 120 |
Total power, kW | 34,75 |
Working pressure, MPa | 0.6 |
Dimensions LxWxH, mm | 7346x990x1700 |
Weight, kg | 2300 |