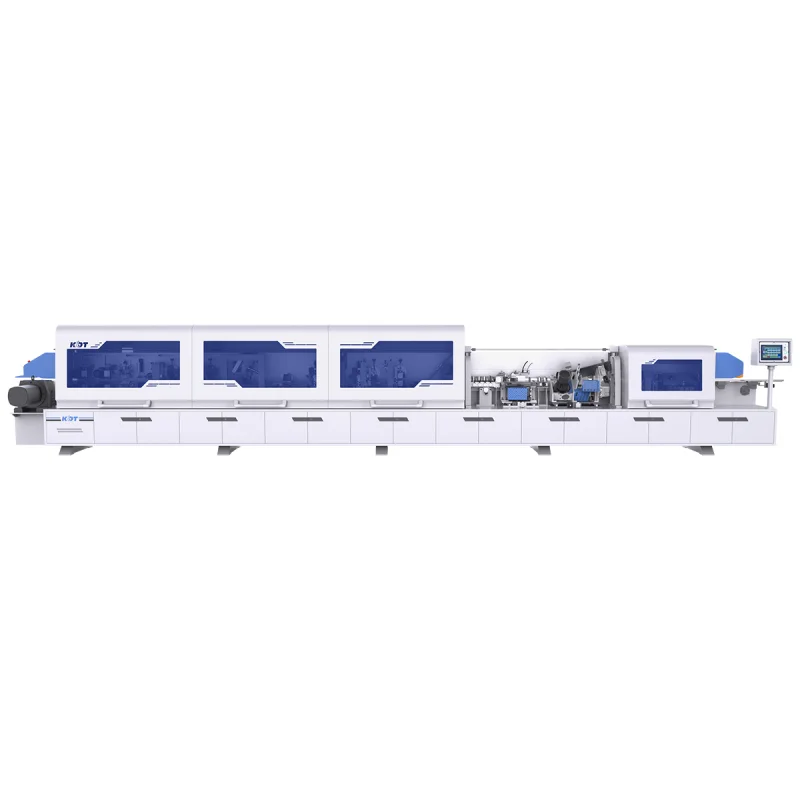
Technical Specifications
Edge thickness 0°, mm | 0,4-3 |
Edge thickness 45°, mm | 0,45-1,5 |
Feed speed, m/min | Straight:15-24; Bevel:15-18 |
Workpiece thickness 45°, mm | 9-25 |
Machine units | 1. Unit of preliminary milling and formation of a bevel. 2. Clamping unit. 3. End cutting unit. 4. The first milling unit for removing overhangs. 5. The second milling unit for removing overhangs. 6. Node contouring (rounds). 7. The first scraping unit with radius knives. 8. The second scraping unit with radius knives. 9. Scraping unit with straight knives. 10. First polishing unit. 11. Second polishing unit. |
Minimum part size, mm | Straight:120x90; Bevel:150x150 |
Workpiece thickness 0°, mm | 9-60 |
Workpiece width, mm | Straight:≥90; Bevel:≥150 |
Workpiece length, mm | Straight:≥120; Bevel:≥150 |
Total power, kW | 42,8 |
Working pressure, MPa | 0.6 |
Dimensions LxWxH, mm | 10292x990x1960 |
Weight, kg | 3000 |
Automatic edge banding machine KE-399
Purpose :
Automatic edge banding machine KE-399 is designed for simultaneous banding of straight edges of furniture boards and blanks with synthetic roll material. The machine allows you to get a product with three different options for gluing the edge. Example of a partial 45° bevel for 16mm and 18mm panels. Example of a partial 45° bevel of a 25 mm thick panel. Example of a partial 45° bevel finished panel . Machine components Unit of preliminary milling and formation of a bevel. Clamping unit. Trimming unit. The first milling unit for removing overhangs. Second milling unit for removing overhangs. Contouring unit (rounds). The first scraping unit with radius knives. The second scraping unit with radius knives. Scraping unit with straight knives First polishing unit. Second polishing unit.
Distinctive features :
Feed speed 15-24 m/min for straight parts, 15-18 m/min for beveled parts; Control panel "Touch screen"; Feed line with heating (not installed on machines with milling); Built-in waypoint control for contactless control of processing units; Possibility of programming technological breaks; Individual frequency converter for each working node; Lighting in the protective cabin; Limit switches on the doors in the protective cabin; Pneumatic shutter on the glue roller, prevents it from getting dirty; Adjustment of the front and rear overhangs of the edge from the control panel; Execution according to CE standards.

machine bed - The bed of the edge banding machine has the form of a rigid box with the necessary stiffening ribs, which guarantees the exact location of all nodes during the entire period of operation .

Remote Control - The machine is controlled using a special remote control equipped with an industrial display with a “Touch screen” system .

technological breaks - Possibility of programming technological interruptions of glue bath heating .

face pre - milling unit - Unit for pre-milling the end of the part before gluing the edge onto the formed surface. It is equipped with two motors that carry out the processing of a straight and inclined section .

Clamping unit - The machine has two clamping units. Each pressure unit consists of 5 rollers, which are driven pneumatically, which guarantees an even distribution of forces on the edge during gluing .

glue baths - The machine is equipped with two glue baths with a glue dispensing mechanism - one for straight parts, and the second for parts at an angle of 45° .

facing unit - The end trimming unit is equipped with two high-frequency electric motors, and the movement of the saw units is carried out along special linear guides. The unit is equipped with an automatic lubrication system for the guides .

milling unit - The milling unit consists of two high-frequency electric motors equipped with radius cutters, which allow processing edge material with a thickness of 0.4 - 3.0 mm .

Contouring unit (rounds) - The rounding (contouring) unit is equipped with two high-speed motors and operates successfully at a speed of 18 m/min. There are four possible operation schemes for the unit .

radius cycle - The first and second scraping units are equipped with two carbide radius knives, which, after milling the edge, remove a thin layer from the milled part of the edge and remove the kinematic wave, as a result we get a smooth processed surfac .

flat cycle - The direct scraping unit is equipped with two hard-alloy straight knives (adhesive scraper), which carry out edge processing at the joints with the part .

polishing unit - A double polishing unit polishes the processed part of the edge; high quality is achieved through an oscillation system driven by pneumatic cylinders. To impart a final shine to the edge, a unit for applying polishing liquid is installed .

pressure tape - The pressure band instead of rollers guarantees precise and reliable positioning of the workpiece in all stages of edging .

clamping traverse - The mechanism for lifting/lowering the clamping traverse is equipped with an electric drive, which ensures fast and accurate installation to the required thickness of the part .

automatic lubrication of the end assembly - The centralized lubrication unit automatically lubricates the guides of the trimming unit .

electrical components according to CE standard - The electrical components are made in accordance with CE standards .

Noise isolation - The doors of the machine cabin are sheathed with a layer of sound insulation made from foamed polyurethane foam, which allows you to achieve comfortable work with the equipment .
Technical Specifications
Edge thickness 0°, mm | 0,4-3 |
Edge thickness 45°, mm | 0,45-1,5 |
Feed speed, m/min | Straight:15-24; Bevel:15-18 |
Workpiece thickness 45°, mm | 9-25 |
Machine units | 1. Unit of preliminary milling and formation of a bevel. 2. Clamping unit. 3. End cutting unit. 4. The first milling unit for removing overhangs. 5. The second milling unit for removing overhangs. 6. Node contouring (rounds). 7. The first scraping unit with radius knives. 8. The second scraping unit with radius knives. 9. Scraping unit with straight knives. 10. First polishing unit. 11. Second polishing unit. |
Minimum part size, mm | Straight:120x90; Bevel:150x150 |
Workpiece thickness 0°, mm | 9-60 |
Workpiece width, mm | Straight:≥90; Bevel:≥150 |
Workpiece length, mm | Straight:≥120; Bevel:≥150 |
Total power, kW | 42,8 |
Working pressure, MPa | 0.6 |
Dimensions LxWxH, mm | 10292x990x1960 |
Weight, kg | 3000 |