
Technical Specifications
Feed speed, m/min | 15-23 |
Machine units | 1. Joint joint. 2. Clamping unit. 3. Facing unit. 4. Milling unit for removing overhangs. 5. Knot contouring (rounds). 6. Scraping unit with radius knives. 7. Scraping unit with straight knives. 8. Polishing unit. |
Minimum part size, mm | 120x95 |
Edge thickness, mm | 0.4-3 |
Workpiece thickness, mm | 10-60 |
Workpiece width, mm | ≥ 95 |
Workpiece length, mm | ≥ 120 |
Total power, kW | 22 |
Working pressure, MPa | 0.6 |
Dimensions LxWxH, mm | 5880x830x1730 |
Weight, kg | 2300 |
Automatic edge banding machine KE-665JSKA
Purpose :
The KE-665JSKA automatic edge banding machine of the pass-through type with an upper glue tank and pneumatic shifting of nodes is designed for simultaneous veneering of straight edges of furniture boards and blanks with synthetic roll material. Machine components Joint knot. Clamping knot. Ending knot. Milling unit for removing overhangs. Knot contouring (rounds). Scraping unit with radius knives. Scraping unit with straight blades. polishing unit.
Distinctive features :
Feed speed 15-23 m/min; Upper glue bath ; Automatic changeover to 2 different edge thicknesses by quickly pressing the corresponding button on the machine control screen; Automatic changeover to 4 different workpiece thicknesses by quickly pressing the corresponding button on the machine control screen (with memory); Infrared lamp for heating the end face of the workpiece; Conveyor feed with encoder system; edge counter; Reinforced conveyor; 5 pressure rollers with scrapers; Pneumatic mechanism for removing scraping chips from the workpiece; Control panel "Touch screen"; Built-in waypoint control for non-contact control of processing units; Possibility of programming technological breaks; Individual frequency converter for each working node; Lighting in the protective cabin; Limit switches on the doors in the protective cabin; Stock dispenser rod prevents damage to machine components during operation; Pneumatic shutter on the glue roller, prevents it from getting dirty; Adjustment of the front and rear overhangs of the edge from the control panel; Fine-tuning counters are installed on all nodes.

machine bed - The bed of the edge banding machine has the form of a rigid box with the necessary stiffening ribs, which guarantees the exact location of all nodes during the entire period of operation .

Remote Control - The machine is controlled using a special remote control equipped with an industrial display with a “Touch screen” system .

technological breaks - Possibility of programming technological interruptions of glue bath heating .

shoe guide - The wall thickness of the conveyor guide shoes has been increased to 15 mm .

rod dispenser - The workpiece feed dispenser rod controls the minimum distance between workpieces, preventing damage to machine components during operation .

steel columns of the upper pressure beam - The new design of the upper beam columns of increased rigidity and special geometry, developed by the engineers of the KDT plant, provides high strength support .
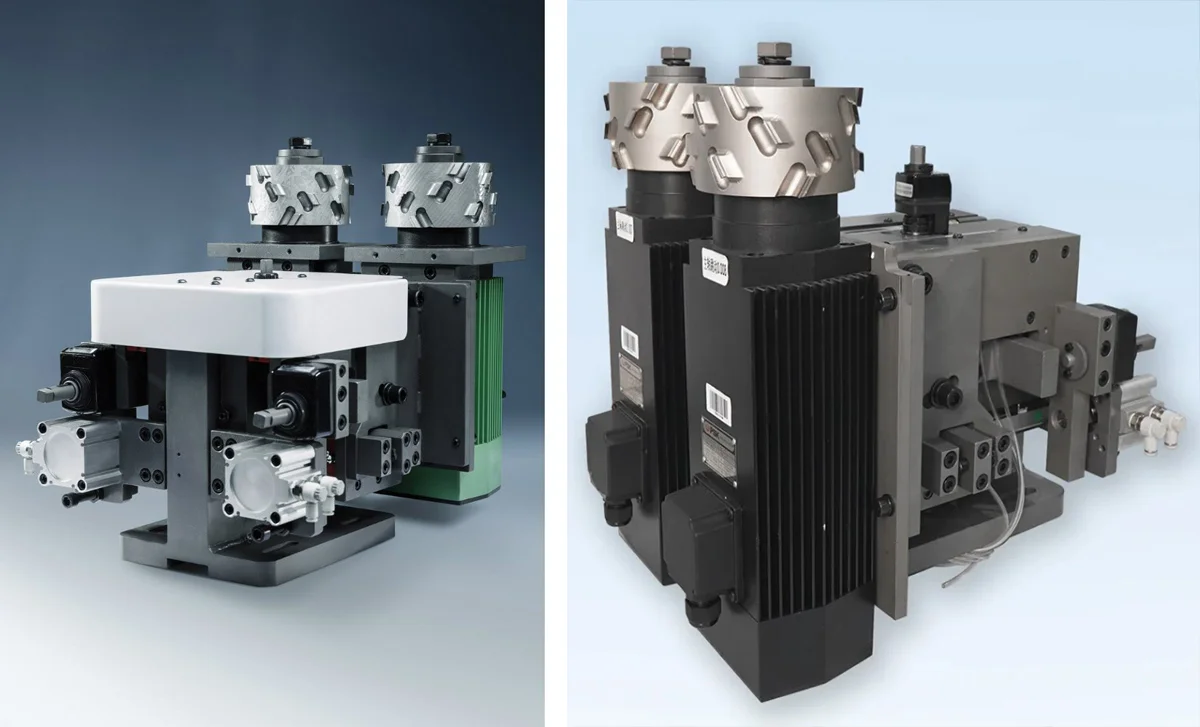
joiner unit - The jointing unit is equipped with two high-frequency motors, which ensures high-quality processing of the end face of the material before gluing the edge. Pre-milling copes with the “step” from the scoring saw, chips .

billet end heating - Preheating the end face of the workpiece for better adhesion .

Clamping unit - The pressing unit consists of 5 rollers, which are driven by pneumatics, which guarantees an even distribution of forces on the edge during gluing .

upper glue bath - Automatic top gluing tank with pre-melting glue, 5 liter capacity. Glue is dosed and does not overheat during machine downtime. The viewing window allows you to control the presence of glue .

glue hopper - The machine is equipped withautomatic pneumatic loading of granulated glue. At the bottom of the machine frame there is a large hopperfor 12 .

facing unit - The end trimming unit is equipped with two high-frequency electric motors, and the movement of the saw units is carried out along special linear guides .

milling unit - The milling unit consists of two high-frequency electric motors equipped with radius cutters, which allow processing edge material with a thickness of 0.4 - 3.0 mm .

contouring unit - The contouring unit (rounds) is equipped with two high-speed motors and successfully runs at a speed of 23 m/min. Four schemes of work are possible .
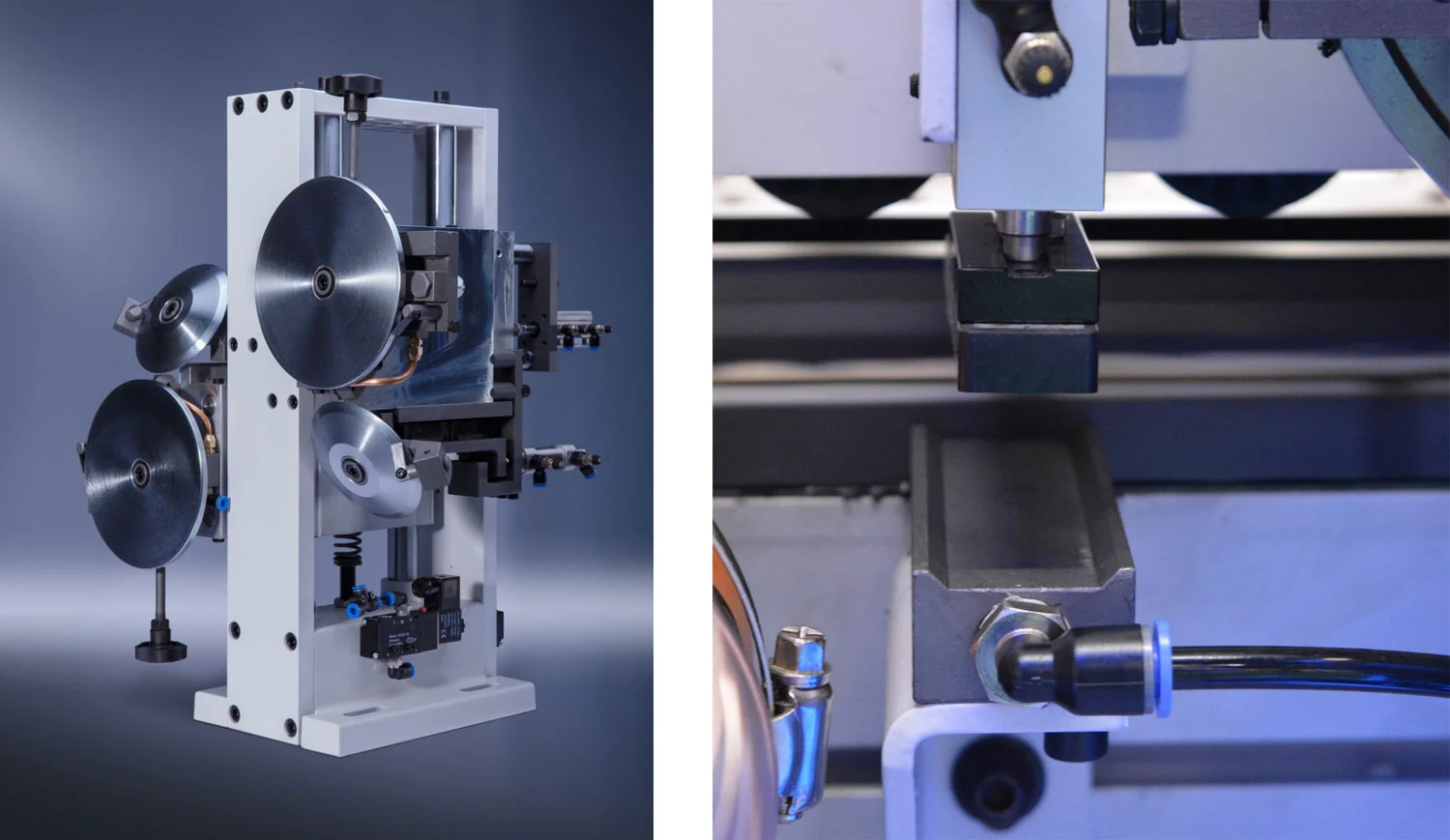
radius cycle - Radial scraping with two carbide radius knives, which, after milling a 2.0 mm thick edge, remove a thin layer from the milled part of the edge, as a result we get a smooth machined surface .

flat cycle - The direct scraping unit is equipped with two hard-alloy straight knives (glue scraper), which carry out edge processing at the joints with the part .
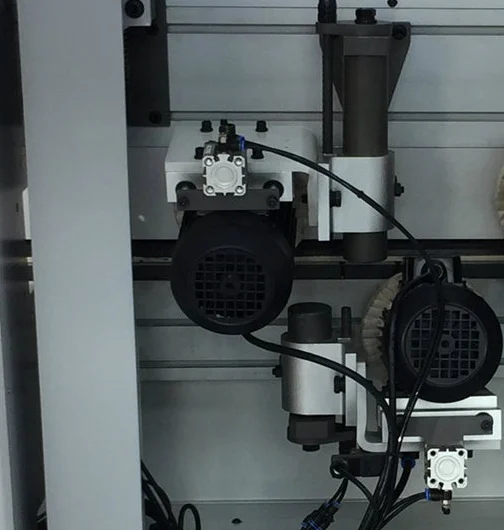
polishing unit - The polishing unit polishesthe processed part of the edge, high quality is achieved throughan oscillation system driven by pneumatic cylinders .

clamping traverse - The mechanism for lifting/lowering the clamping traverse is equipped with an electric drive, which ensures fast and accurate installation to the required thickness of the part .

automatic lubrication of the end assembly - The centralized lubrication unit automatically lubricates the guides of the trimming unit .

automatic conveyor lubrication - Automatic lubrication of the conveyor is carried out by an electric pump .

electrical components according to CE standard - Electrical components of the world's leading manufacturer - Siemens, are made in accordance with CE standards .

Noise isolation - The doors of the machine cabin are sheathed with a layer of noise insulation made from foamed polyurethane foam, which allows you to achieve comfortable work with the equipment .
Technical Specifications
Feed speed, m/min | 15-23 |
Machine units | 1. Joint joint. 2. Clamping unit. 3. Facing unit. 4. Milling unit for removing overhangs. 5. Knot contouring (rounds). 6. Scraping unit with radius knives. 7. Scraping unit with straight knives. 8. Polishing unit. |
Minimum part size, mm | 120x95 |
Edge thickness, mm | 0.4-3 |
Workpiece thickness, mm | 10-60 |
Workpiece width, mm | ≥ 95 |
Workpiece length, mm | ≥ 120 |
Total power, kW | 22 |
Working pressure, MPa | 0.6 |
Dimensions LxWxH, mm | 5880x830x1730 |
Weight, kg | 2300 |